One of the foundations of the Toyota Production System is the concept of Standard Processes. This works using basic work instructions up to a point, but what happens when you don’t have a standard product due to the diversity of customer options and configurations?
In these situations, it becomes increasingly difficult to have a standard process because each product can be different. Each product might have a selection of options that needs to be fitted in different ways or use different component parts depending on the interaction between the options.
VisualFactory™ creates and deploys dynamic work instructions that automatically modify what is shown to the operator to make sure that the process they are following creates the configured product defined by the customer order. Orders are downloaded from the ERP and work instructions are generated in real-time with the correct configurations, including component part number, for that particular order.
VisualFactory™ has evolved to satisfy each of the 4 Toyota Production System Ms of manufacturing which are Manpower, Machines, Materials, and Methods.
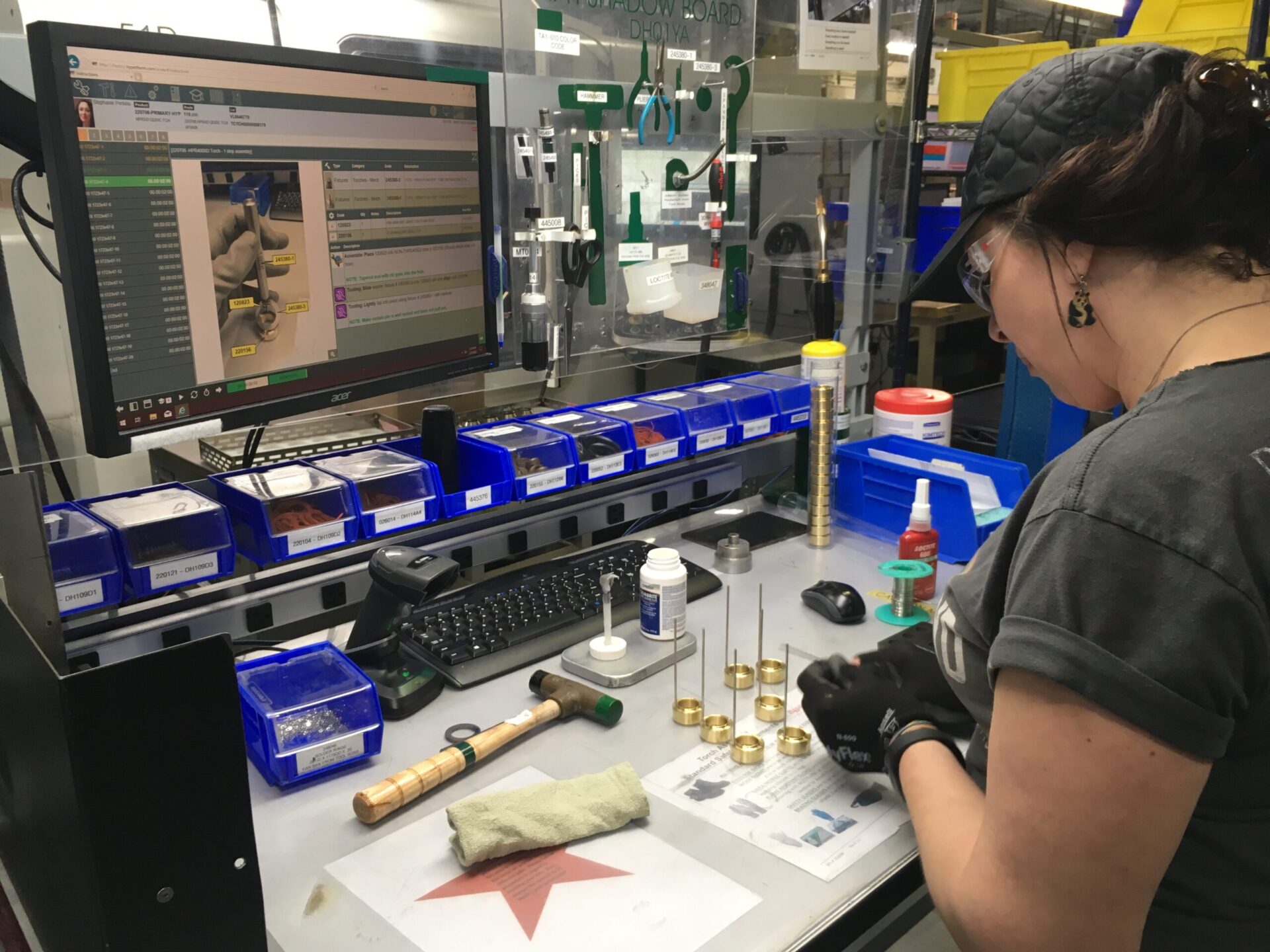
VisualFactory™ validates that the operators have the correct training and skills to undertake the work assigned to them. If they do not have the correct training, they won’t be allowed to continue.
Machines represent the tooling and equipment to be used. As the operator selects the tool identified in the work instruction, they can scan the asset code and VisualFactory™ will automatically check the calibration records to ensure that the equipment is fit for purpose.
Every time that a material or component is identified, the operator can verify that they are using the correct part as laid out in the instructions using barcode labels or build to light. VisualFactory can also record information like serials numbers for component traceability.
VisualFactory ensures that the operators are using the right method by requiring them to complete each activity in sequence as they work through the production process. Any step that they fail to carry out the process as laid out, results in immediate feedback for the operator. Where difficulties arise, they can raise a Production Issue with an Andon call or enter the product into a Rework Process.
In this way, we ensure that each of the four elements are addressed at every step of your production process. You will reduce quality defects, with assembly defects being eliminated. Defects such as component failures are found much earlier in the process, leading to huge increases in right-first-time quality. This provides you with a no faults forward approach in place for your complex configure to order assembly.
Adherence to the optimal process leads to increased productivity. Our customers report an increase in productivity between 5 and 15% because their optimal process is always being used. If you are interested in finding out how VisualFactory can help you achieve your optimal production process, then please contact us for a free demonstration.